In the printing industry, Finishing refers to the additional processes that are done after the ink has been applied to the paper. Some of these processes can be done while the printing is still on the press (inline), but most are done after the printing has been completed (offline).
Many printing companies have a Finishing department that offers a variety of services to improve the quality and appearance of printed materials. Bindery operations, which involve cutting, folding, and binding printed pieces, are a large part of finishing work. For this reason, some printers use the term “Finishing and Bindery” or “Finishing and Binding” to describe all post-printing activities.
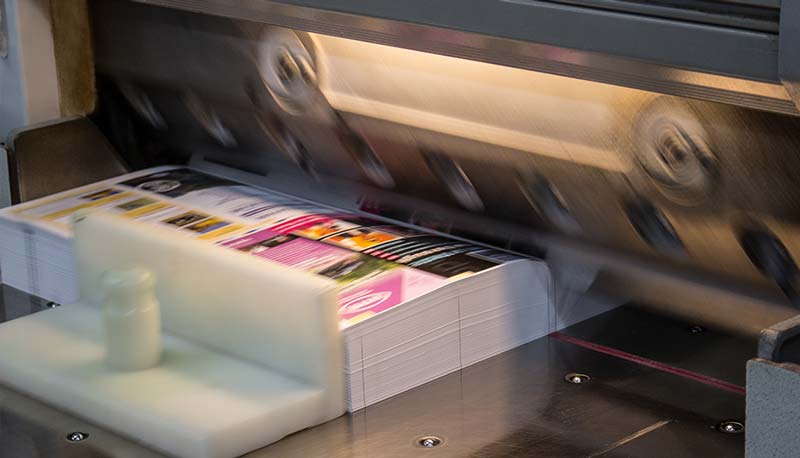
Some of the common finishing services in the printing industry
Aqueous coating – Aqueous coating is a water-based clear-coat that is applied to printed pieces to help protect the ink and paper against minor scuffs and abrasions. It provides a glossy finish that enhances the colors and details of the printed piece, while also offering protection against scratches, stains, and fading. Aqueous coating is a cost-effective option for adding a professional and durable finish to printed materials such as brochures, business cards, postcards, and packaging.
Binding – Binding is a term used to describe the process of gathering and fastening separate sheets or signatures together. It can be as simple as placing a single staple through a set of documents, but it typically refers to the creation of durable books and booklets. Popular binding methods include perfect binding, saddle-stitching, spiral/coil binding, wire-o binding, pro-click binding, and hardcover binding. Binding can also involve the insertion of components into a ringed binder.
Collating – Collating is the process of gathering and arranging individual sheets or other printed components into a specific order or sequence. This ensures that each set contains the correct pages or parts in the right order, making it easier for readers to follow and understand the content. Collating is an important step in the printing and publishing process, as it helps ensure the accuracy and consistency of printed materials.
Cutting & Trimming – Cutting and trimming in printing refers to the process of using a sharp blade or shear to reduce a printed piece to its desired size or shape. This can involve removing excess paper along crop marks, separating pieces that have been printed as multiple images per sheet, or trimming the open edges of a book to create evenly aligned pages. This step is important for ensuring that printed materials have a clean, professional appearance and are ready for use or distribution.
Die-cutting – Die-cutting is a process that involves using a thin, sharp blade that has been pre-formed into a specific pattern or outline to cut paper, cardstock, labelstock, or other substrates into various shapes. This process allows for precise and intricate cuts, creating custom shapes and designs. Die-cutting is commonly used in the printing industry for creating unique packaging, labels, business cards, and other printed materials. It adds a professional and polished look to printed pieces, making them stand out and grab attention.
Drilling – Drilling refers to the process of creating round holes in paper using a rotating bit, such as the hole patterns needed for sheets and dividers placed into ringed binders. This process is often used to create precise and consistent holes for organizing and filing documents in binders, notebooks, or other storage systems. Drilling can be done manually with a handheld drill or using automated equipment for larger volumes. It is a common finishing operation in the printing and binding industry.
Foil stamping – Foil stamping is a specialized process that uses heat and pressure to apply a metallic foil design to a printed piece. The foil is usually gold, silver, or copper, but a variety of colors are available. Foil stamping adds elegance and distinction to printed materials and can be combined with embossing to create a raised metallic design. This process is commonly used for business cards, invitations, and packaging to create a luxurious and eye-catching finish.
Folding – Folding in printing is a process that bends a printed piece so that it lies flat upon itself. This can serve multiple purposes, including reducing the physical size of the printed piece so it can fit into something else like an envelope, packaging, or display rack. A smaller size can also make certain printed items easier to handle and distribute. Folding is also used as a design technique to create separate panels from a single sheet, such as for a brochure or invitation. There are various folding styles available, including the popular c-fold, z-fold, roll fold, gatefold, and mini fold.
Laminating – Laminating is a process that involves bonding a clear plastic film onto printed material to protect it from stains, smudges, moisture, wrinkles, and tears. This greatly improves the durability of the printed item. Lamination is available in various finishes, such as gloss, matte, or soft-touch. In addition to adding a protective layer, a gloss laminate enhances the vibrancy of the ink colors. Lamination is a popular choice for printed items that need to withstand heavy use, such as educational materials, flip charts, book covers, restaurant and bar menus, maps, and consumer displays.
Padding Glue – Padding is a process that involves applying a flexible adhesive along one edge of a stack of same-sized sheets. The adhesive secures the sheets as a unit, but allows the topmost sheet to be easily removed as needed. In most cases, padded sheets incorporate a chipboard backer for rigidity. Common examples include notepads, memo pads, and order pads. This process is commonly used for creating convenient and easy-to-use pads of paper for various purposes.
Perforating – Perforating is a process that creates a series of very fine holes in paper or cardstock, usually along a straight line, to allow a portion of the printed piece to be easily detached by hand. This is used for various purposes, such as coupons, ID cards, response cards, and remittance slips. Perforating makes it easy to tear off a section of a printed piece while keeping the rest intact. This is especially useful for items like coupons or response cards that need to be separated from a larger piece of paper.
Scoring – Scoring is a printing process that involves making a crease in paper or cardstock to make it easier to fold. This is done to improve the appearance of the fold and provide a consistent guideline for the fold. Scoring is typically used on heavyweight papers and cardstock to ensure a clean and professional-looking fold.
Sequential numbering – Sequential numbering is a printing process that involves the printing of identification numbers in ascending or descending order so that each printed unit receives its own unique number. This unique number can appear in one position or in multiple positions on each document. Sequential numbering provides a method for easy reference and a high degree of accounting control. It is frequently used on contracts, invoices, purchase orders, quote forms, checks, raffle tickets, contest entries, or virtually any printed item that needs unique identification.
Shrink-Wrapping – Shrink-wrapping is a packaging method that encloses bundles of printed materials within a transparent plastic film. The application of heat causes the film to shrink around the printing, securing it tightly. This not only provides a layer of protection but also creates convenient-sized packs, making it easier to handle and distribute the printed pieces. Shrink-wrapping is a cost-effective way to package printed materials, ensuring they remain in good condition during transit and storage.
UV-coating – UV-coating is a process where a tough, clear-coat is applied over printed materials to improve their resilience and appearance. This coating is applied in liquid form and then exposed to Ultra-Violet (UV) light which bonds and dries it instantly. UV-coating provides a glossy finish that enhances the colors and details of the printed piece, while also offering protection against scratches, stains, and fading. It is commonly used for items like brochures, business cards, postcards, and packaging to give them a professional and durable finish.
If you have any questions about printing, feel free to reach out to us at 718-928-6888 or submit our quote request form. We’re here to assist you in any way we can.
Take care!
Jeff @ New York Printing Center